1 引言
莱钢中小型轧钢生产线于97年建成投产,主要生产圆钢、弹簧扁钢、槽钢和螺纹钢。该生产线plc控制系统由abb公司提供,其自动控制系统采用abb masterpiece 200/1 plc控制系统,实现了18架轧机以及冷床、冷剪和码垛机的自动控制。基础自动化系统采用abb公司的rmc200轧钢控制系统,它是一个开放型集散控制系统,由一套mp200/1过程站和一套as520操作员站组成。过程站由一个cpu机架带一个i/o机架组成,cpu机架上安装了cpu模板dspc172、内存模板dsmb176以及32通道的di/do模板,通过通讯模板dscs140连接到masterbus300总线上,与其它过程站进行通讯,i/o机架由总线扩展模块dsbc172实现总线扩展。
操作员站采用hp-unix工作站,并通过实时加速器板连接到masterbus300的冗余接口,通过它操作人员可直接对现场设备进行监控,主要功能有:(1)轧钢生产设备的启停(2)设备数据设定和实时监控(3)事件与报警清单的显示与打印等。系统的主要画面有启动画面、设定画面、维护画面、事件画面和报警画面。系统配置图如图1所示。
2 plc诊断轧钢生产设备故障的基本原理
轧钢设备的故障信号有数字量和模拟量之分,plc采用不同的方法对这两种信号对应的故障进行诊断。
2.1 基于数字量信号的故障诊断
plc对数字量信号的识别是通过其数字量输入模块完成的。plc控制轧钢生产设备时,设备中的压力、温度、液位、行程数字及操作按钮等数字量传感器与plc的输入端子相连,每个输入端子在plc的数据区中分配有一个“位”,每个“位”在内存中为一个地址。读取plc输入位的状态值可作为识别数字量故障信号的根据。诊断数字量故障的过程,实质就是将plc正常的输入位状态值与相应的输入位的实际状态值相比较的过程。如果二者比较的结果是一致的,则表明设备处于正常工况,不一致则表明对应输入位的设备部位处于故障工况。这就是plc诊断基于数字量信号故障的基本原理。这种诊断方法,故障定位准确,可进行实时在线诊断。通过plc的图形功能块编程,还可将故障诊断融入过程控制,达到保护轧钢设备的目的。
2.2 基于模拟量信号的故障诊断
plc对模拟量信号的识别是通过plc的模拟量输入输出模块来完成的。模拟量输入输出模块采用a/d转换原理,输入端接收来自传感器或变送器的模拟信号,输出端输出的模拟信号作用于plc的控制对象。plc诊断模拟量故障的过程,实质就是将在相应a/d通道读到的监测信号的模拟量的实际值与系统允许的极限值相比较的过程。如果比较的结果是实际值远离极限值,则表明轧钢生产设备对应的受监控部位处于正常状态,如果实际值接近或达到极限值,则为不正常状态。判断故障发生与否的极限值根据实际系统相应的参数变化范围确定,利用plc上的模拟量设定开关可**设置该极限值。
当模拟量的实际值达到模拟量设定开关的设定值,plc还能按照一定的逻辑关系启动开关量模块上的输出位,或者从plc的通讯口主动发起通讯,从而输出故障诊断的结果,并据此实现对轧钢生产设备的控制。
2.3 基于中断方式的故障诊断
plc的中断方式有:
(1) 输入中断;
(2) 间隔定时器中断;
(3)高速计数器中断。其中,输入中断特别适合于轧钢生产设备的故障诊断。它对应于工业操作站的硬中断,属于外部中断,但plc的输入中断可用plc的外部指令来屏蔽。将轧钢生产设备的故障信号作为plc的输入中断源,一旦出现故障信号,cpu立即响应,停止正在执行的程序,转到中断子程序中去,即可方便地对故障进行处理。它与直接利用plc的内部逻辑完成故障诊断的不同之处在于:采用输入中断处理故障时,可停止plc主程序的执行过程,而直接利用plc的输入和内部逻辑处理故障时,plc的主程序仍处于运行状态。因此,要根据故障对轧钢生产设备的影响程度选择合适的故障诊断方式。plc的输入中断方式对后果严重的突发故障的处理特别有用。
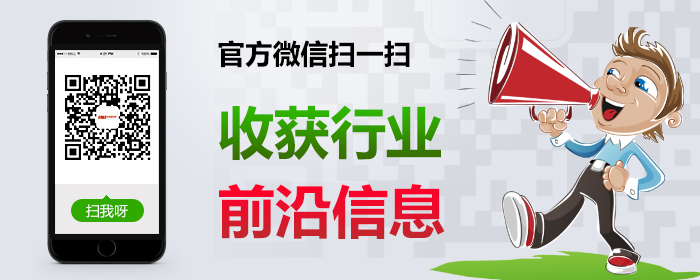