目前,此自动翻板机已经在一汽轿车股份有限公司调试运行,各个环节都已达到预期的设计要求。综合起来,在自动翻板机中使用PLC进行控制,具有**性高,稳定性好,易于控制和调试等诸多优点;同时,用PLC对触摸屏进行控制,不仅实现了对设备运转的实时监控,更重要的是提供了人机交互界面,使后台的程序控制转化为直观的按钮操作,极大的方便了操作人员的使用。 在汽车制造行业中,车身覆盖件在加工成形过程中,都需要事先对其进行上下翻转,以保证后续工序的顺利进行。以往要完成这一工序,主要依靠工人的手工操作,既费时又费力;如果采用自动翻板机,不但可以减轻劳动强度,而且还大大的提高了工作效率。但是,目前此类设备多数依赖进口,引进设备投资大,且维修费用高。鉴于这些方面的原因,如何能够自主的开发自动翻板机就具有非常重要的现实意义。
本文介绍了作者在为国内某大型汽车生产制造厂家研制的自动翻版机中,如何利用PLC来实现翻板机的自动控制。
1 设备构成及动作实现
1.1 翻板机的整体结构(如图1):
图1 翻板机结构图
1.驱动电机 2.送料小车 3.活动台板 4.侧挡 5.上横梁 6.夹紧梁
1.2 工作流程:
自动翻板机整体上分为侧工作台部分和翻转圆盘部分。侧工作台部分主要包括驱动电机和送料小车,用来完成送料或取料任务;翻转圆盘部分主要包括夹紧梁、侧挡和翻转圆盘,分别由液压马达和液压油缸来驱动,用来完成夹紧和翻料任务。
自动翻板机的工作流程是:物料由侧工作台送入翻转圆盘,夹紧梁向下夹紧物料后进行翻转,达到合适位置时,停止翻转,撤销夹紧,仍由侧工作台将物料取出、运走。
对系统的功能要**:能够根据物料吨位的不同适当的调整夹紧力的大小,确保物料能够被可靠地夹紧、翻转;能够方便地进行参数设置、手动调试;具有实时监控功能。
2 控制系统的组成及程序设计
2.1 控制系统组成
图2 控制系统组成
触摸屏和控制面板做为人机交互界面,其中触摸屏通过RS422数据接口与PLC进行通讯,为操作人员提供方便的在线监控、参数输入以及手动调试功能;模拟量输入、输出模块(A/D、D/A)通过其侧面的数据线与PLC相连接,在自动翻板机工作时,时刻检测液压系统的压力和温度,用来控制液压元件在一定的温度环境下,按照设定的压力值完成预期的动作;PLC是整个控制系统的核心部分,主要负责开关量信号的输入、输出控制,模拟量数据的计算处理以及触摸屏信号的响应;另外PLC还通过数据线与扩展模块相连接,扩充了控制系统的输出点数。
软件方面采用MITSUBISHI公司的GX Developer编程软件进行PLC程序设计;用MITSUBISHI公司的FXDU编程软件进行触摸屏程序设计。
2.2 系统的程序设计
自动翻板机设计为手动和自动两种工作模式,可以在控制面板上进行两种模式的自由切换
图3
手动工作模式主要用来调试设备,检测翻板机各机械部分的运动协调状况;在触摸屏上为分别每个运动机构设置了启动按钮,直接操作这些按钮就可以实现对应部分的点动动作。自动模式是自动翻板机的正常工作模式,也是程序设计的关键所在。在设计这一工作模式时,我们将系统的整个自动工作过程划分成若干阶段,每个阶段都独立完成一部分的工作,然后再由PLC将各个阶段按照一定的顺序有机的结合起来,构成完整的自动程序。这样做的目的:一是有利于程序的编制,增加程序的可读性,尤其是为将来设备调试和维修提供方便;二是确保翻板机的各个工作环节更加**、更加可靠。实践证明,这个办法确实行之有效。自动工作流程如图所示。
下面就以夹紧阶段为例来说明自动翻板机系统的程序设计。夹紧是确保整个自动工作顺利进行的关键所在,故将这一工作单独划分为一个阶段来玩成。进行夹紧之前,在触摸屏上设定相应大小的压力值,由PLC对设定的数值进行处理;D/A模块把处理的结果转化为电压信号,输出给比例阀或比例泵,完成液压系统的压力或流量设定。在夹紧过程中,PLC控制A/D模块对液压系统的实际工作压力进行实时检测,并同时与设定的压力值进行比较,当达到预设的压力值时,夹紧动作就自动停止,然后向下一阶段发出夹紧完成信号。其他阶段的设计思路与夹紧阶段类似,这里不再赘述。
另外,由于液压系统的长时间工作或者周围空气环境的变化,必然会导致液压油的温度发生变化,所以自动翻板机还需要具有温度检测与自动调节功能,以保证液压元件正常工作。这部分工作由A/D模块来完成,当检测到油温超出设定的温度范围后,自动启动相应的温度调节装置,使液压系统温度控制在一定范围之内。
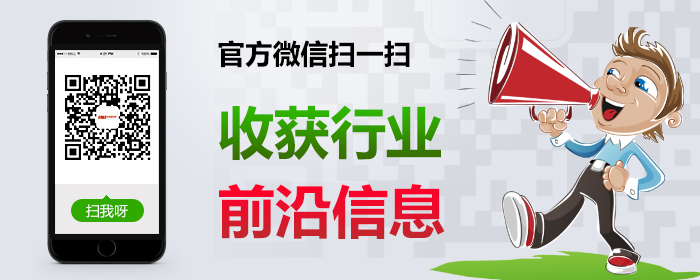