技术背景——技术现状
关于现场总线型多参量在线油液分析仪,传统的设备管理理论认为:由于油液在保存上具有相对的保质期限,同时使用时其品质特性也会发生劣化变质。为了预防油液劣化、变质对设备运行造成破坏性影响或需要通过油液的状态变化来诊断设备磨损的情况时,我们就需要大量油液分析工作。
随着设备向大型、微型、高速、重载、自动化、成套化、多功能化、环境节能性方向发展,设备的维修成本和停机损失也随之急剧增加,因此对设备运行的可靠性和经济性必然提出更高的要求,促使工业界将以实施状态监测为举措的状态检修提到了更为迫切的地位上。通过对设备的润滑状态的实时监测,可大大降低因油品劣化造成磨损失效,有效地延长设备使用寿命,减少停机损失,可以通过油液的参数变化反映出设备的磨损状态,保证设备长期稳定处于*佳运行状态,预防和避免产生事故,特别是机损人亡的重大事故。
案例1:
南方某大型柴油机发电厂引进中速大功率柴油机数十台,设备总值高达10多亿美元。由于其恶劣的工作条件,在设备投入使用后不久即多次发生烧瓦、拉缸、曲轴断裂的事故。这些事故造成的损失统计如下:一次烧瓦事故,仅换瓦费*低要5500马克,一次拉缸损失*低要7~8万人民币。而*大的一次断轴事故损失更高达330万人民币之多!这其中还未包括停机损失(以1万马力的单机机组为例。每停机1小时即损失人民币1万元。该厂装机总容量为32.8万千瓦)。这些事故及产生的后果,终于使该厂设备管理人员认识到油液监测的不可或缺的作用。自实施油液监测后,十余年来,科学的监测数据使该厂主要设备的各类故障得到了早期预报与预防,再未发生过重大设备事故。该厂每年平均为每台设备支付的监测费用不到1万元,仅据96~98年3年统计,累计节约的备件维修费已超过1000余万元。油品使用寿命延长了三倍多,节油费达240万元。
案例2:
某合资企业以550万美元引进的自动生产线,是全厂的关键设备。使用的润滑油主要为齿轮油和液压油。油箱体积不大,一直执行定期换油制,每次换油费用并不高,而如果一旦发生意外停机和事故,将对全厂正常生产带来严重后果,停机损失巨大。在**次大修过后仅2个月时间即发现运行参数出现异常,面临停机危险。该生产线停机1小时即损失人民币3.2万元。此时,设备管理人员求助于油液监测技术,问题得到了及时解决。而这样的生产线在该厂共有5条,设备总值近3000万美元。这次故障诊断为其它生产线的正常运行提供了宝贵的借鉴经验。
案例3:
近几年来, 汽轮发电机组容量不断增大, 蒸汽参数不断提高。国外先进技术的引进, 机组的本体结构及技术性能也有较大的飞跃,同时也对轴承润滑油的要求亦不断提高, 因为它直接关系到机组运行的平稳、可靠和**。由于对汽轮发电机组润滑油系统的认识及管理水平没有及时跟上, 仍停留在小机组定期抽样监测的手工管理层次上, 导致润滑油油质清洁度普遍较差, 长期不能满足大容量机组的要求, 造成汽轮发电机组轴颈频繁拉毛磨损的例子比比皆是。
如某电厂300MW机组第1次大修期间因用火焊切割发电机后轴承进油管垂直管段后未清理而使金属渣随润滑油进入轴承内, 造成轴瓦和轴颈严重磨损, 被迫在现场对轴颈进行车削处理并更换轴瓦。
另有某电厂600MW 机组由于油系统不清洁, 油路被污染, 造成6号、8号瓦磨损严重, 相应的轴颈拉毛, 顶轴油泵损坏失压低速时不能建立起正常油膜, 使启动调试时间延长了7个月。据有关资料介绍, 从1989年~1994年机组轴颈进行电刷镀的多达12台次。
常见油液油质分析工作方式有两大类:
1)离线式理化指标分析
2)在线式实时监测仪器
技术背景——离线式理化指标分析
工作方式:
人工采样油料后进行铁谱、光谱、颗粒计数、黏度等多项理化指标分析;
典型产品:美国OSA公司的OSAII全自动综合油料分析监测仪;
技术特点:
配以专家系统对检验结果进行分析,检验结果准确可靠。
技术背景——在线式实时监测仪器
工作方式:检测探头被直接安装在被测设备上,通过对润滑油温度、粘度、密度等指标进行实时监测;
典型传感器及相关产品:美国西储大学(CWRU)的基于MEMS的多传感器探头及在此基础上生产制造的FPOS4000在线多参数油液分析仪。
技术特点:实时、在线、自动化、网络化监测。无人化管理,节约大量人力成本。
技术背景——必要性(1)
麻省理工大学(M.I.T)的研究标明,设备故障70%与摩擦面蜕化有关,由于无法直接对摩擦面进行实时监测,使用油液 分析仪 对摩擦面进行间接连续监测成为所有技术中的**。 通过油液分析不仅可以了解摩擦面的劣化趋势,还可以同时完成设备运行状态的实时连续监视
通过对各参量的监测,可以实现以下目标:
(一)实现润滑油油质和旋转机械磨损的实时在线监测,通过监测油液温度、电导率等参数的突然变化,实现机械故障的早期预警;提高企业自动化水平。
(二)通过对密度的实时连续监测,可以得到该参量的变化趋势,一旦得到连续增加的趋势,就可以得到油的氧化、添加物损失与工作环境改变的联动等信息,进而可以根据退化速度对润滑油作健康评估;并进一步通过激励来延长润滑油的生命周期。
(三)润滑油的粘度是温度的函数,通过连续、实时监测得到的润滑油的粘度和温度参数,可以进一步根据润滑油的粘度决定当前润滑油的温度是否适合,从而采取进一步措施改变润滑油的温度,使润滑油处于*佳工作状态,为设备的*佳负载提供决策依据。
(四)通过在过滤网的前后分别安装油液分析仪,通过两组传感器测量结果的比较,可以进一步得到如下信息:
1) 油液在单循环回路中的劣化情况;
2)滤网效能的下降趋势,过滤网何时需要清洗或更换。
(五)节能、减排、降耗;节约维修成本、检测成本和劳动力成本,通过油液分析可以延长换液周期,并对周期内油液劣化预警。
(六)可帮助用户实现油液质量在线批次管理,及时发现各批次油液的质量差异,为更换不同品牌的油液决策提供数据支持。
(七)通过对油液质量的连续监测建立油液品质与旋转机械磨损和运行工况状态的联动跟踪,为日后建立旋转机械设备健康状态与油液状态相关联的故障诊断模型提供硬件设备支持和数据积累。
(八)实现现场监测数据的网络化共享,为生产和管理提供决策依据。
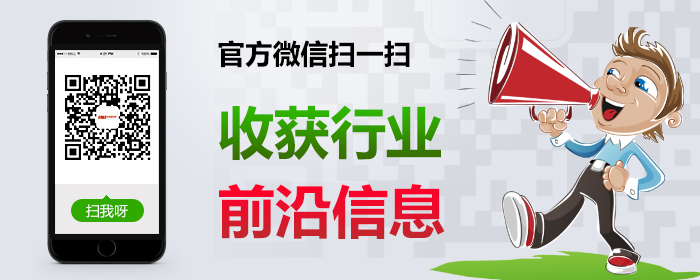